La NASA ha recentemente sviluppato una nuova lega metallica che migliora drasticamente la resistenza e la durata delle componenti utilizzate nell’aviazione e nell’esplorazione spaziale, ottenendo prestazioni migliori e più durature.
Il materiale, nato dalla combinazione di leghe metalliche e particelle ceramiche, si è dimostrato oltre 600 volte più resistente dei metalli attualmente utilizzati.
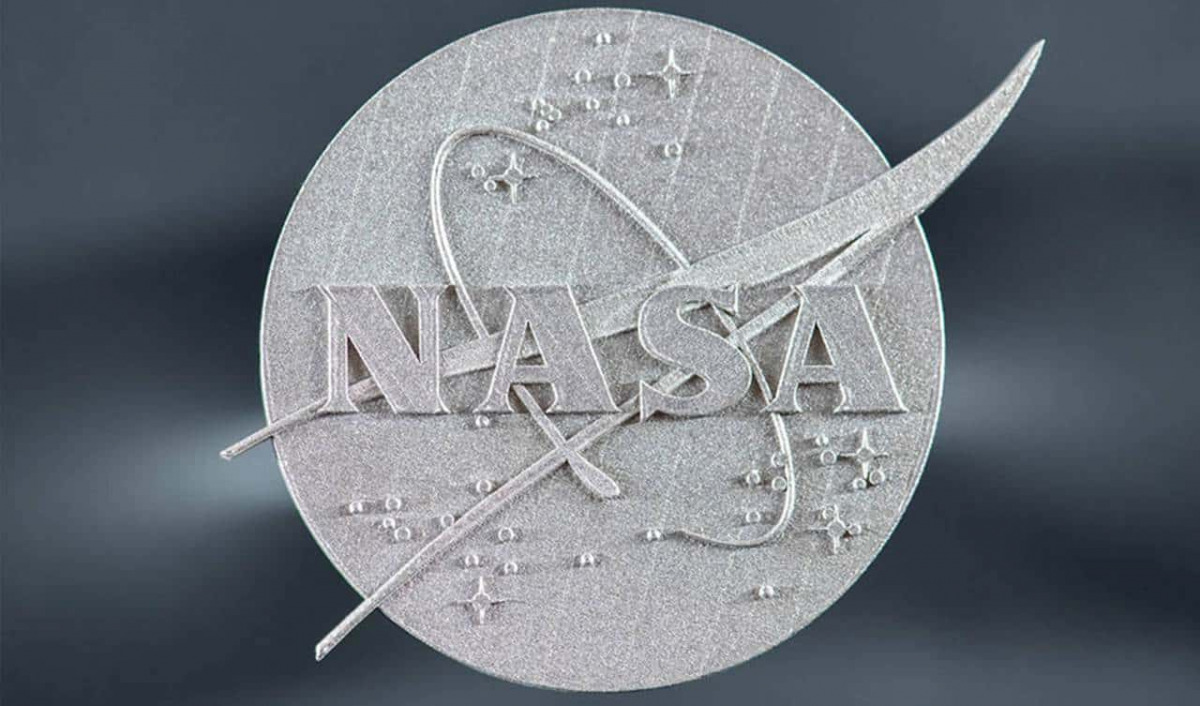
GRX-810: la lega stampabile in 3D progettata per ambienti estremi
La lega GRX-810 della NASA è una lega rinforzata con dispersione di ossido (ODS) che può sopportare temperature superiori a 2.000 gradi Fahrenheit: non solo è più malleabile, ma può sopravvivere più di 1.000 volte rispetto alle leghe di ultima generazione esistenti. Questa nuova lega può essere utilizzata per costruire le componenti dei veicoli aerospaziali, destinati a supportare le alte temperature che si manifestano all’interno di aerei e motori a razzo.
“Le particelle di ossido su scala nanometrica permettono degli incredibili vantaggi in termini di prestazioni”, ha dichiarato Dale Hopkins, vice responsabile del progetto Transformational Tools and Technologies della NASA. La National Aeronautics and Space Administration prevede inizialmente di utilizzare il materiale, attualmente chiamato GRX-810, per stampare “iniettori, ugelli, cupole di combustione” e tutte le parti di aerei e astronavi che devono essere in grado di sopportare un calore estremo senza guastarsi.
I vantaggi della lega super-resistente
La nuova lega porterà molti vantaggi che, prima di questa scoperta, erano impossibili da raggiungere con la stampante 3D. Per sviluppare la lega GRX-810, i ricercatori della NASA hanno utilizzato modelli computazionali per determinare la composizione della lega, in seguito hanno utilizzato la stampa 3D per disperdere uniformemente ossidi in scala nanometrica in tutta la lega. Questo processo di produzione non solo è molto più efficiente, ma è anche più economico e meno inquinante rispetto ai metodi convenzionali.
I modelli computazionali mostrano ai ricercatori non solo i tipi di metallo da incorporare, ma anche la quantità di ciascun elemento da inserire nella composizione: “Le prestazioni di questa lega dimostrano chiaramente la maturità dello strumento di modellazione e la sua capacità di produrre risultati significativi”, ha dichiarato Steve Arnold, responsabile della disciplina tecnica materiali e strutture della NASA Glenn.
Secondo il dottor Tim Smith, ricercatore del Glenn Research Center della NASA, le parti stampate hanno dimensioni limitate a pochi centimetri a causa della specifica macchina laser utilizzata per stampare in 3D il GRX-810. Un problema che sarà presto risolto secondo Smith, questo perché i ricercatori stanno cambiando il processo di stampa 3D, adottando una nuova tecnica in grado di utilizzare una maggiore quantità di energia su un involucro molto più grande.
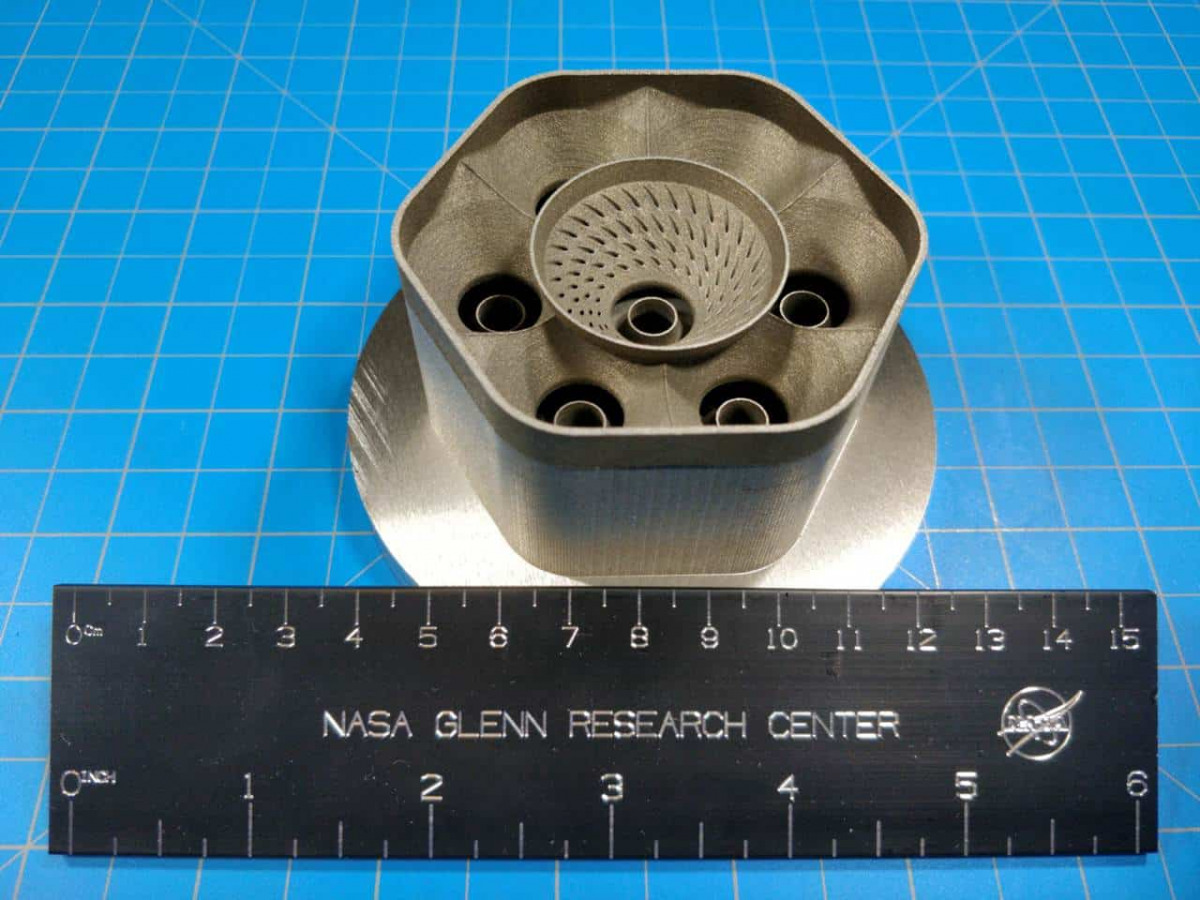
Michael Shepard, vicepresidente del segmento Aerospazio e Difesa di 3D Systems, ha dichiarato che il successo delle proprietà del GRX-810 della NASA, testimoniano l’incredibile potenziale di questa nuova superlega, non solo in termini di prestazioni ma anche a livello puramente produttivo.
La super-resistenza del GRX-810
“Il nostro lavoro con questo materiale fornito dalla NASA sottolinea il nostro impegno a spingere i confini della produzione additiva (stampa 3D) e a consentire la produzione di componenti aerospaziali di nuova generazione. Siamo entusiasti di far parte delle prime fasi di questo entusiasmante sviluppo e non vediamo l’ora di sbloccare nuove possibilità con il GRX-810″.
Il materiale è in grado di resistere particolarmente anche alle radiazioni, questo vuol dire che le componenti presenti in ambienti con radiazioni particolarmente elevate, come i reattori a fissione o a fusione, potranno trarre un grande vantaggio dalla dispersione di questi ossidi. Secondo Smith, la NASA e altri hanno esplorato leghe simili in passato, ma è stata una combinazione di elementi specifici e l’utilizzo della stampante 3D a dare al GRX-810 proprietà così eccezionali rispetto ai materiali già esistenti.
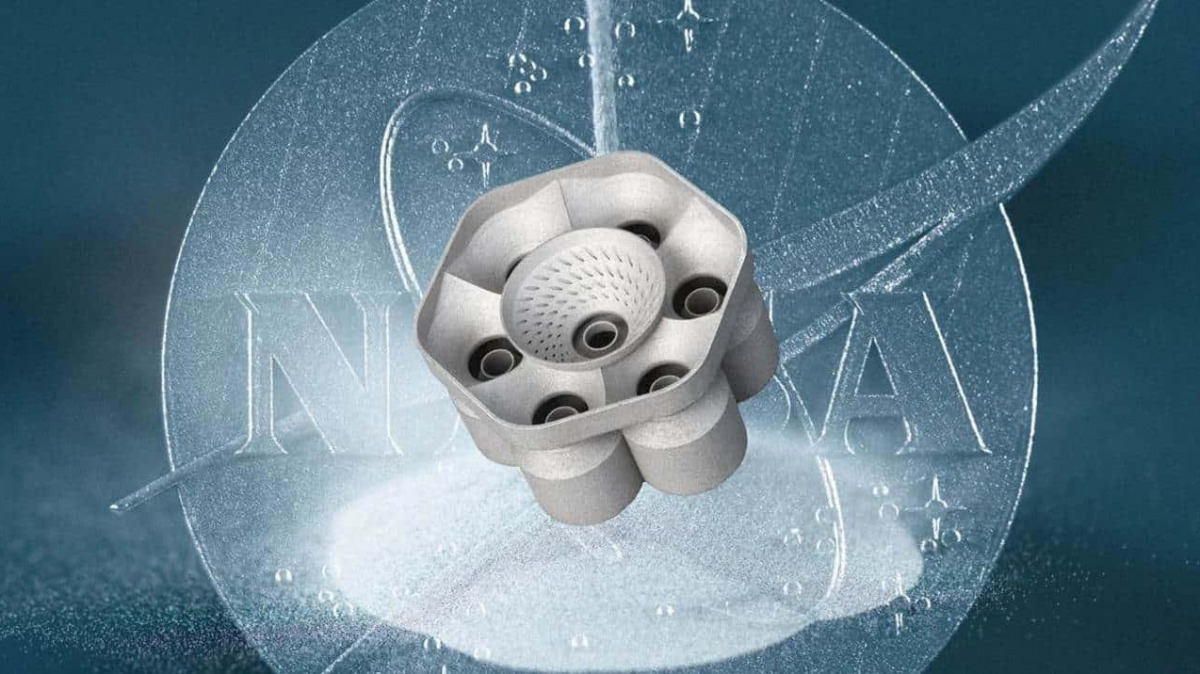
Per scoprire la resistenza delle varie leghe viene utilizzato il “creep test”, che consiste nel collocare il materiale in un ambiente ad alta temperatura, sottoponendolo a un carico statico, un peso o una pressione, e di attendere per vedere quanto tempo impiega il materiale a rompersi. Nello studio, Smith e i suoi colleghi hanno testato il GRX-810 contro leghe ad alte prestazioni esistenti in un creep test da 2.000 gradi Fahrenheit e con un carico fino a 3.000 libbre per pollice quadrato. Le migliori leghe esistenti hanno resistito fino a circa 10 ore, il GRX-810 ha resistito per 6.500 ore.
“Questa nuova lega è solo un esempio di come il progetto Transformational Tools and Technologies fornisca soluzioni innovative attraverso la ricerca fondamentale e strumenti trasversali.” Il prossimo passo di Smith e dei suoi colleghi sarà quello di continuare a studiare il processo di produzione della nuova lega super-resistente per capire come introdurla al più presto nell’industria: il GRX-810 potrebbe essere solo l’inizio.